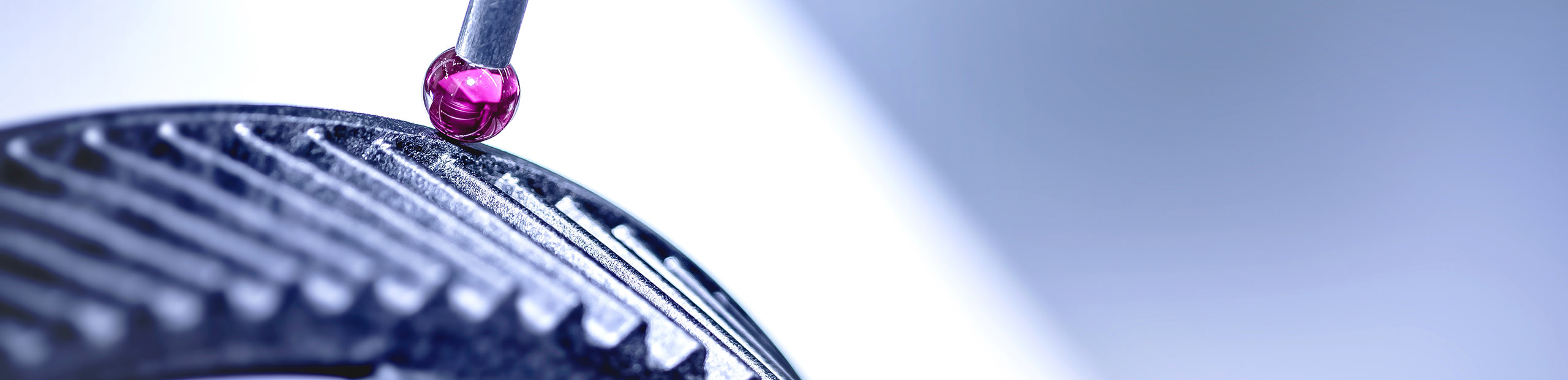
Industrial measurement technology and non-destructive computer tomography in the company’s own GAUDLITZ measuring center.
We work out goal-oriented, efficient strategies, in order to supply you with high-precision results more quickly.
The process-accompanying product validation in our own measuring center is one of the special strengths that we at GAUDLITZ can offer our customers directly at the production site. On the basis of our high-precision industrial and computer tomographic measuring equipment, not only can we carry out non-destructive testing of components, but also perform analyses and evaluations straight away. This puts us in a position to shorten product development times, ensure quality and thus lower costs.
- Professional analyses of your components and modules
- Cost-efficient process integration of all measurement tasks
- Component optimization in terms of geometry, material and tolerance
- Reliable measurements thanks to decade-long expertise from our team of experts.
- Full solutions for your measurement tasks thanks to the application of state-of-the-art metrology
Contour and surface measurement – reliable roughness and contour measurements.
With the application of our surface measuring device “Perthometer Concept” from the company Mahr, your components can be examined for roughness values and contours in numerous fields of application – with a large number of measurement tasks if needed. Thanks to a special zoom function, error-free detailed examinations can be performed of different parts. A clear advantage, because the processing times of the components are often shortened.
- Error-free detailed examinations of components using the latest feeler and zoom technologies
- Determining of angles, radii, distances and coordinates in the context of contour measurement
- Presentation and archiving of roughness and contour measurements in a conclusive results form
Gear measurement – more analysis possibilities by means of the latest double flank rolling testing technology.
The double flank rolling testing technique has proved itself to be a fast and simple method for the functional testing of gears. Thanks to this industrial measurement process, we can carry out precise testing for rolling defects (Fi´), rolling skips (fi´), rolling concentricity (Fr), and axial distances. Unlike other measuring technologies, the double flank rolling testing device is specially designed for small test pieces and/or plastic gears, thanks to its low gauging forces and precision. Tests for individual defects are carried out on our coordinate measuring device Zeiss Prismo Vast with an integrated rotary table unit.
- Measurement of screws, spur gears, pinions and helical gears with the Frenco double flank rolling testing device ZWP 06
- Tests for individual defects using the Prismo Vast coordinate measuring device
flying | Between tips | |
---|---|---|
Axial distance | 12-80 mm | 12-80 mm |
Axial distance with reduction attachment | >1 mm | >1 mm |
Max. Test piece average with counter bearing | 80 mm | 80 mm |
Gauging force setting | 0-5 N | 0-5 N |
Area of application | Small workpieces and plastic gears | Small workpieces and plastic gears |
Optical measurements – extensive statements about complex geometries.
Optical measurement is becoming more and more important in industrial production. Unlike the tactile measuring processes, it can be used to measure large-area geometries and components. With the CNC 250 and the tried-and-tested OGP® MeasureXTM software, we possess a high-precision measuring device, which can be supplemented with CAD conversion, contour, analysis, report generation and statistics programs as needed. Thanks to a variety of additional lenses and lighting technologies, a scale resolution of up to 0.5 µm is possible. Special guidance and bearing technology ensures the reliability of our measurements across the whole XYZ travel range.
- Contactless, optical measurements with OGP® SmartScope® CNC 250
- The latest DSP (Digital Signal Processing) technology for short testing times and fast travel movements
- Coordinate measuring machine Eclipse from Zeiss with the camera system VISCAN
Range | mm | Measurement accuracy in µ | |
---|---|---|---|
CNC 250 | X axise | 250 | 2.0 + 4L/1,000 |
CNC 250 | Y axis | 150 | 2.0 + 4L/1,000 |
CNC 250 | Z axis | 200 | 3.0 + 5L/1,000 |
Tactile measurements – point information accurate to the micrometer.
The so-called tactile measuring processes – in which the material surface is swept, point by point, with touch-activated sensors – are excellently suited to determining shape, position and dimensions. A clear advantage over other industrial measuring process is the high precision of the scanning system, which makes it possible to carry out measurements in the micrometer range.
We use the following software:
- Calypso
- Gear Pro
- Holos
- Umess UX
- Dimension
- Reverse Engineering
Zeiss – Prismo Vast
Thanks to the use of the rotary table unit, we are in a position to carry out checks for individual defects in gears using Gear Pro – on the common rotationally symmetric components. Various quality-determining parameters are measured to ascertain the gear quality. Such as, for example, profile and flank line deviations, and division faults.
Zeiss – Eclipse
Due to the high complexity of components in medical technology, automobile construction and industry, it is not enough to apply either tactile or optical sensor technology on its own. With the ViSCAN 2D optical probe, we have combined tactile and optical measuring tasks in a single device. In addition to this, a VAST XXT Scanning Sensor is at our disposal for tactile scanning.
Zeiss UMC 850
Our UMC 850 is used for the tactile measurement of larger components. The measurement range here spans from the X axis, with 850 mm, to the Y axis, with 1,200 mm, to the Z axis with 600 mm.